Triradial vs Crosscut Mainsails – Part 2
Mar 20, 2024
By Keven Piper, Bay Sails
Part 1 takes a look at triradial vs crosscut mains. Part 2 considers speed, longevity and cost.
In most one design classes like Stars or Etchells, where intense effort is made by sail designers to make the fastest sails, a very high proportion of the sail shape is imparted with tapering of the edges of the assembled panels. Sailmakers call this broadseaming, but it should be more accurately described as seam curves. This converting of flat pieces of cloth into a smoothly curved three-dimensional surface requires that the edges of each panel is super accurately cut and assembled. This sounds difficult to do with scissors, and it is, since the amounts of curve are measured in fractions of millimetres in some cases. The magic of modern sailmaking is the equipment we use to cut these panels today. The venerable Gerber cutter that cut many of my sails in the past and the newer CNC laser cutters can quickly cut an entire table lay of sailcloth in minutes with 0.1mm of accuracy over the length of the 16m long table. That is more accurate than a pencil line is thick. If you have access to excellent cutting, you should definitely use it.
So back to a Triradial sail vs a Crosscut sails for shaping a sail. In the case of the mainsail in question, mainsails tend to be slightly flatter than headsails, but they have a much more variable shape from the foot to the head. This desired vertical shape change means we want to have a stable moulded-in shape to the sail, so that the leech remains stable, and the draft position doesn’t move around with different wind pressure loads. The more stable the shape, the faster and longer lasting the sail. That means we generally want as much shape moulded into the sail as possible, so we want a high ratio of seam curve shape to luff curve shape.
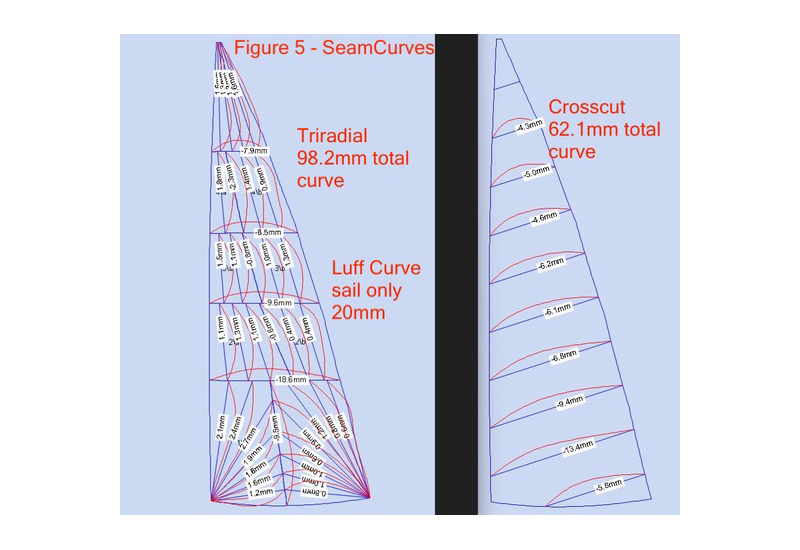
The Crosscut version of this mainsail ends up with 62.1mm of total seam curve in the sail, and the Triradial Quilt Cut version uses 98.2mm to fit the cloth over the same desired design mould shape. 155% more seam curve is built into Triradial sail than the Crosscut sail would use. This will mean that the Triradial sail will be more stable, regardless of the stretch implications in shape change. Compare this to the predominantly luff curve designed sail with only 20mm (or less) of seam curve.
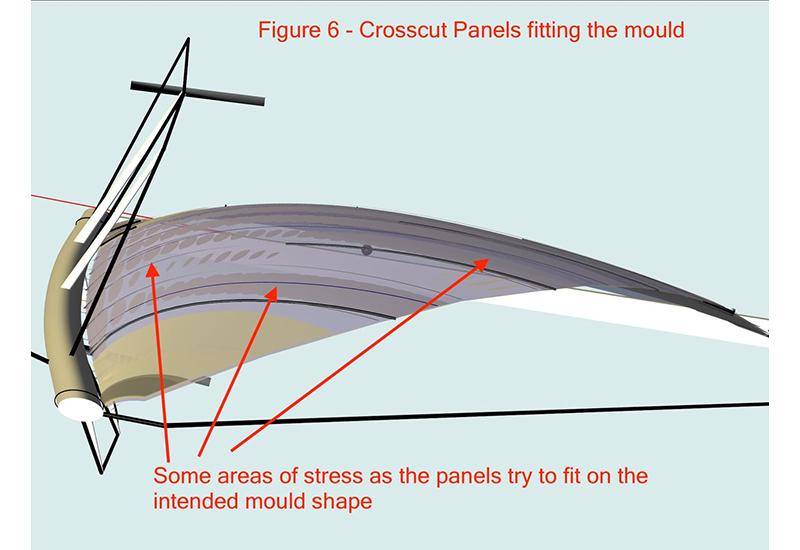
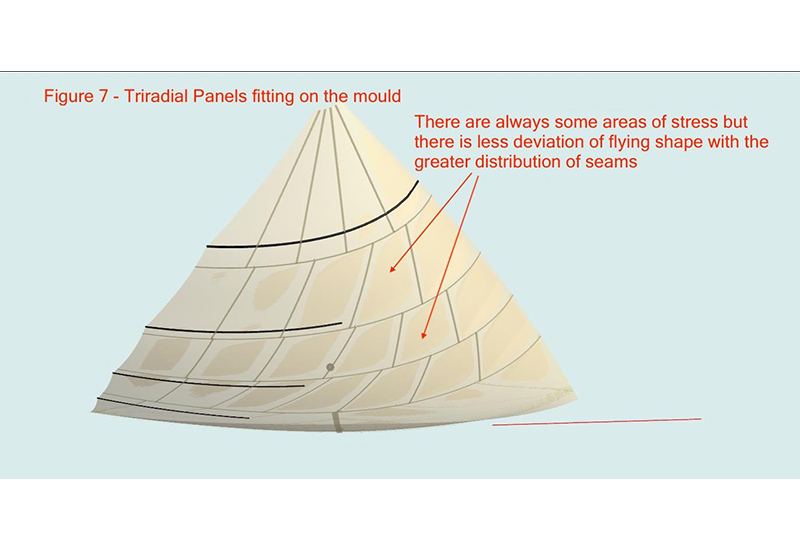
As you can see in the fit of the flat panels onto the three-dimensionally curved surface, there is always some strain as the flat cloth is trying to replicate the surface. The more opportunity for curved panels to create a more faithful representation of the designed shape that we have developed in the design and testing program.
So why do most of the sailmakers make their racing woven mainsails crosscut? There are probably many reasons:
- Cost of design is higher if they already have a good selling crosscut design.
- Cost of cloth is slightly higher and wastage is also higher.
- More assembly time for a triradial.
- They backed into their design over time with recuts which are easier to replicate with crosscut designs. This is quite common with sailmakers, as some are more comfortable working with small modifications to existing design rather than updating the entire design.
Costs do get in the way of actually selling a product, but in a one design class that allows the most expensive cost is no issue technologies in the headsail, why not invest in a better performing mainsail?
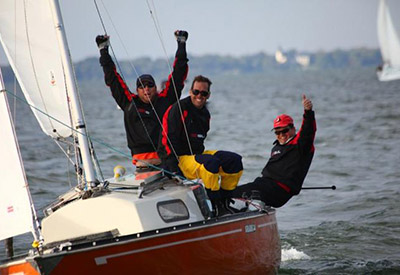
Keven Piper, two-time Shark 24 World Champion, founded Hamilton, ON-based Bay Sails in 1998. Email: baysails@gmail.com