Triradial vs Crosscut Mainsails – Part 1
Mar 6, 2024
I had a very interesting conversation with a client just yesterday. They have a popular one design class that limits mainsail cloth to woven polyester (PET – polyethylene terephthalate) in a minimum weight of 300g/m2. The client also believed that the class mandated crosscut panel cuts because “all of the other sailmakers” were only making the mains in crosscut layouts. Some classes do have such rules, quite a few in the United Kingdom, but a careful reading of the class rules showed no such limitations.
The pointed question asked of me was “Why are they all making crosscut mainsails, if triradial or other vertical cut sails are better at holding their shape?”. I find this an interesting discussion, so this is my explanation.
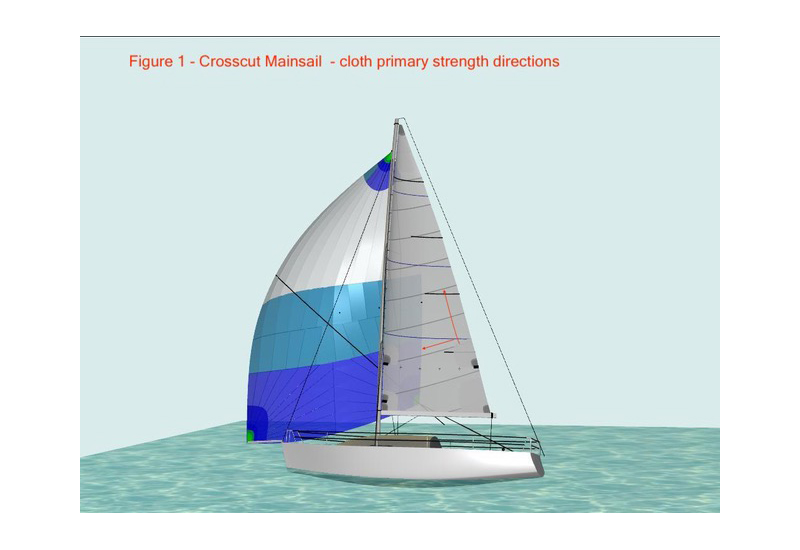
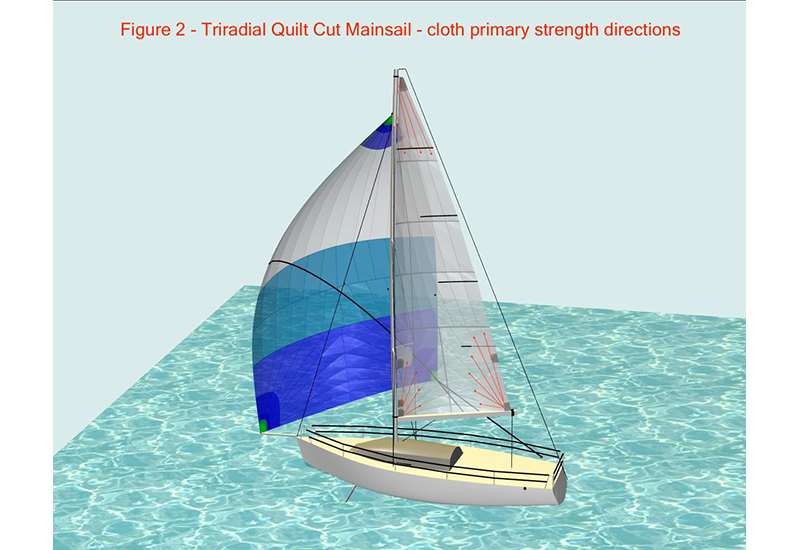
Are radially cut sails inherently better at holding their shape? I have covered part of this topic before. Check it out here: https://sailingincanada.ca/tech/sail-tech/keven-talks-sails-crosscut-vs-triradial-sail-cutting/
Essentially, new weaving technology has given us more choices of heavier weights of very high-performance woven cloth meant for radial construction from all the major sailcloth producers. This wasn’t something that was readily available more than a decade ago and may have influenced the previous sail development in the class and the other sailmakers haven’t looked at making improvements to their existing sail designs. Design time costs money.
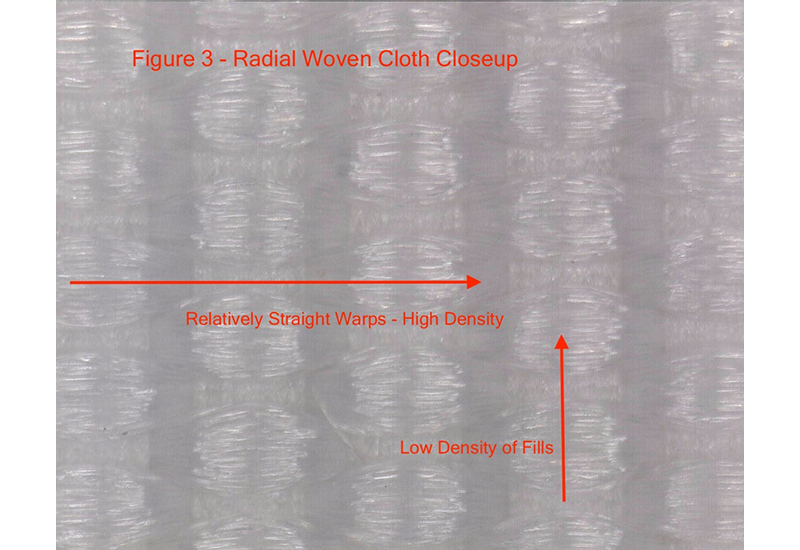
Consider the design advantages of the radial panel layout over the crosscut. Sails are shaped using two major methods:
The most common method is to induce camber with edge excess curves, also known as luff curve. Effectively, this type of sail will have a very minor amount of moulded (seamed) shape build into the sail body, and the extra cloth added to primarily the luff of the sail is forced into the sail from the luff edge. This is common with many “moulded” or “one piece” sails, because there are very few seams that can be shaped, or the gently shaped mould used cannot be as aggressively curved to match the desired flying shape of the sail. This induced camber method is quite easy to build as the very few important assembly and cutting steps is faster and any assembly errors can be faired at the luff curve at the end of sail assembly. This method of design is quite quick, but the sail tends to age prematurely as the shape isn’t well locked in place.
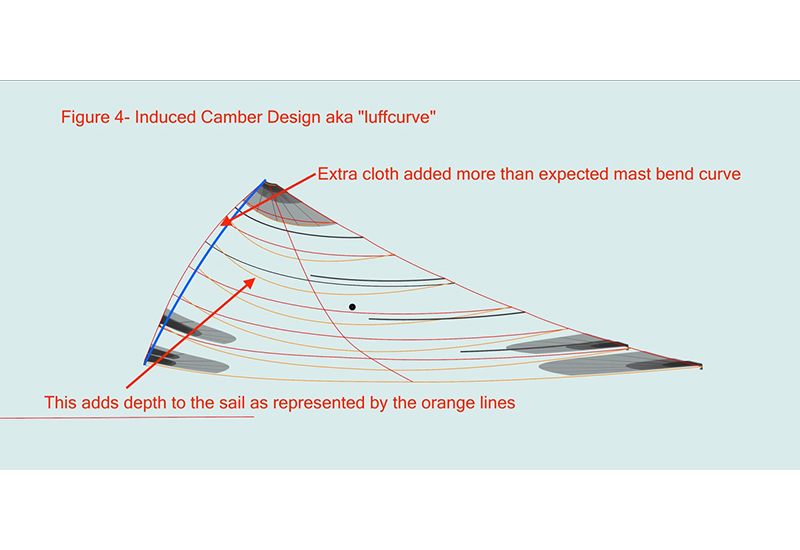
Next time: making flat sailcloth curve and the secrets of broadseaming
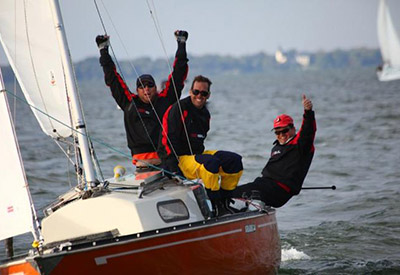
Keven Piper, two-time Shark 24 World Champion, founded Hamilton, ON-based Bay Sails in 1998. Email: baysails@gmail.com