Dissimilar Metal Combination Keel For 68-Foot Modern Classic Cruiser/Racer
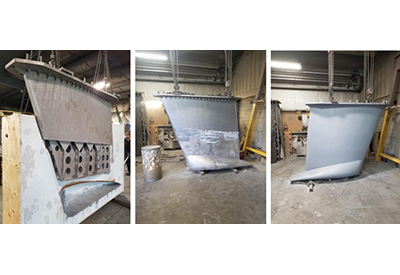
August 17, 2022
Working alongside a US-based designer and boat building company, Burlington ON’s MarsKeel Technology recently provided a dissimilar metal combination keel for a 68-foot modern classic cruiser/racer. The keel consisted of two sections. The upper section was a hollow fabricated steel keel fin (A36/44W) and the lower section was lead cast bulb. The bulb was integrally casted on the fin, which is a hallmark of MarsKeel. An Integrally Cast Bulb (ICB) simplifies the connection between the fin and the bulb. This process has a lower leg on the fin that extends into the bulb making a very secure attachment between the 2 parts.
This project was a collaboration between MarsKeel, Stephens and Waring Yacht Design, and James Betts Enterprises. The designer on the project, Stephens and Waring Yacht Design, offered the construction drawings for both the fabricated keel fin and the lead casting.
Stephens Waring Yacht Design is a custom naval architecture and engineering firm located in Belfast, Maine. MarsKeel has a longstanding relationship with them, and over the years, we have collaborated on several similar projects.
James Betts Enterprises was founded in 1970 and is a multigenerational boat building company. They are known for building yachts for teams competing in America’s Cup, Admiral’s Cup, and Trans Pac.
MarsKeel has maintained understanding, support, and communication with both the builder and designer of this project.
Product Specifications
The upper hollow steel fabricated fin weighed approximately 1,900 lbs, while the lower cast lead section of the lead cast bulb weighed 16,000 lbs. The relatively light upper section allowed the centre of gravity of the keel and yacht to be lowered, creating a higher level of stability for a given weight and draft. Due to this, the ballast weight was saved, yet stability was maintained by replacing some of the keel volumes with lighter steel fabrication.
The upper angle under the top plate was made from fitted high density foam epoxied into place. This was faired smooth to cover all the steel gussets between the bottom of the top plate and the side plates of the keel. This shape mimicked the angle that was first offered in the original keel fin designs. The foam was glassed with one layer of 9 oz fibreglass, faired and coated with Interprotect 200E barrier coat. The joint between the fin and the top of the bulb was covered with 2 layers of 9 ox cloth, overlapped on the seam, then faired into the keel.
MarsKeel Technology assisted the design process by suggesting that the original gusset between the top and side plates be changed from a formed flat bar to many small transverse triangular gussets. MarsKeel made this suggestion because, according to our fabricator, it would be very hard to form to the top of the lead cast bulb and the underside of the top plate at the same time, and it would be hard to keep water out of the void behind it. The designer accepted these changes and redefined the size, spacing, and a number of gussets.
MarsKeel also suggested changing the original vertical bolts or rods down from the bottom.
What made this project complex was the connection between the two materials. Through collaboration and using the combined experience of MarsKeel, the designer, and the builder, challenges were overcome to create a safe and simple design.